Bradyn Antosiewicz ’27 Is Building His Future, One Class, One Precision Component At A Time
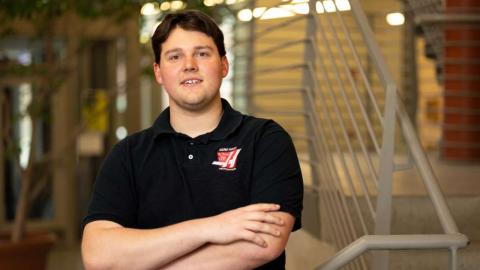
Bradyn Antosiewicz ’27 Is Building His Future, One Class, One Precision Component At A Time
Whether tinkering, fabricating, or assembling, Bradyn Antosiewicz ’27 sees hands-on applications not just as a preference, but as a way of life. And it’s apt to remain that way.
A sustainable product design & innovation (SPDI) major with nearly four years of real-world work experience, Bradyn is what one might say, ahead of the curve.
But that’s not unique for Keene State students in this popular and ranging career field. Unique in New England, the College’s SPDI program combines industrial design, project management, and manufacturing engineering technologies.
Product design and prototyping make up the core pathway, but Keene State students like Bradyn can further focus their studies by adding a SPDI option, such as general engineering or manufacturing engineering.
No matter what the choice, it’s hard to go wrong, says Bradyn, who chose the manufacturing engineering option. “In the program, we partner with professors in learning, and they help us move our education beyond the classroom, and they know the skills we need in this field.”
SPDI students also benefit from a vast network of industry contacts, including Keene State alumni who are in the field and come to the College each year for job fairs.
“I’ve put myself in a good spot, I feel, to be an engineer,” Bradyn says. “Not tomorrow, but early in my career.”
“If it weren’t for meeting one of the graduating seniors through the College, I would not have gotten the job I have at Precitech for real-world experience and to add to my resume. Here I am making things every day while playing with other people’s toys.”
– Bradyn Antosiewicz ’27
“Most of our students graduate with a meaningful internship experience,” says Jared Nelson, associate professor for SPDI. “Then there is that subset of students who hold jobs while enrolled, like Bradyn. That industry experience takes their education to a whole new level.”
As a high school freshman, Bradyn took a machine tool class, enjoyed it, and by his junior year, he had gotten a part-time job at Timken, a global technology leader in engineered bearings and industrial motion. After three years at Timken’s plant in Keene, Bradyn took a paid part-time job at AMTEK Precitech in its Keene facility, manufacturing components for diamond-turning lathes and precision optics processes.
Within 100 miles of Keene State, more than 30 companies thrive in the use of single-point diamond turning machining, thin films, specialty glass, and advanced optics, with Precitech being among them.
Keene State offers a one-year precision optics certificate that provides practical skills to get job-ready quickly. Enrollees learn in the College’s new dedicated optics lab, the Kingsbury Center for Diamond Turning Excellence, on the same high-end ultra-precision lathes used in the field.
Moving to Precitech was a big jump, Bradyn says. “Timken was high production, but a lower mix. We made thousands of parts, many of which were not that different. “Now I manufacture a majority of the components we need in-house.”
For Bradyn, academic flexibility and staying part of a close and vital community mattered when considering college.
“From day one, I could see how much my professors wanted me to succeed. The education and experience I’m getting outside of class will make me more marketable and useful as a new employee starting on day one. I feel like companies that hire Keene State students know and rely on that.”
“Networking and meeting so many students has helped me out big time,” Bradyn says. “If it weren’t for meeting one of the graduating seniors through the College’s Society for Manufacturing Engineers Club during my senior year, I would not have gotten the job I have at Precitech for real-world experience and to add to my resume.
“Connections are huge, and almost everyone at the College is willing to help you succeed.
His parents, Dan and Jen, say they are most proud of the person Bradyn has become, adding, when he’s passionate about something, Bradyn is all in.
“When he learned to play hockey, he built an ice rink in our front yard with his own tool designed to remove snow from the rink,” Dan says. “When he learned to play lacrosse, he and his grandfather designed and built wooden shafts for his lacrosse sticks. When he got into bass fishing, he taught himself how to make rods and lures. He purchased a bass boat and uses his 3D printer to design and fabricate parts to help enhance the boat.”
Bradyn’s classes this semester were Human Factors in Safety, Logical Argumentation, Metrology and CMM, and Product DFMA (Design for Manufacturing and Assembly).
Besides bass fishing, Bradyn enjoys playing ice hockey and spending time outdoors. His first memories of using his hands to fashion items are from when he was a young boy watching and learning in the woodshop of his grandfather Wayne Cotton.
“And here I am, making things while playing with other people’s toys.”
Expensive toys, but for this builder and tinkerer, toys nonetheless.
Learn more about Keene State’s sustainable product design & innovation program